Gross Floor Area: 7,793 m²
Building Composition:
• Ground Floor: Diagnostic and Mammography Departments with 2 MRIs, 3 CTs, 2 Gamma Cameras, 2 Mammography units, and 2 Ultrasound Rooms.
• First Floor: 38-bed Decant Ward with 22 single bedrooms (each with an ensuite) and 4 four-bed bays.
• Second Floor: 36-bed Respiratory and MADU Ward with 12 Very High Dependency Single Rooms (each with an ensuite), 12 step-down single rooms (each with an ensuite), and 3 four-bed bays.
• Third Floor: Plant room.
Services in our scope
PROJECT DESIGN (IO) was subcontracted to coordinate and integrate various electrical systems within the new modular building.
This encompassed all aspects of Electrical, Fire, Nurse Call, and Security systems coordination.
Key Coordination Tasks
• Containment Coordination
• Plantroom Coordination
• Vertical Distribution
• Coordination of 1600Amp Bus-Bar incoming supply
• Coordination of spacialist services
• Coordination of Lighting and Small Power Services
• Provision of construction drawings (shop drawings)
Quantity of Items Modelled
• 723 Lighting Devices
• 1,880 Lighting Fixtures
• 836 Data Devices
• 732 Security Devices
• 662 Nurse Call Devices
• 1,748 Fire Alarm Devices
• 6,558 meters of Containment
Case Study:
Hospital Diagnostic and Inpatient Unit
At PROJECT DESIGN (IO), we were honoured to support a leading hospital in their ambitious project to enhance its capacity and service efficiency with a new 4-storey modular building.
This building, seamlessly linked to the main hospital, includes diagnostic and inpatient facilities designed to improve patient care and operational effectiveness.
How We Make Your Life Better:
• Save Time: Our verified processes mean fewer delays and faster project completion.
• Cut Costs: By avoiding rework and optimising designs, we help you stay within budget.
• Expect Quality: Our expertise ensures that all systems are integrated smoothly.
What You Need to Do:
Contact us today to discuss how we can support your next project.
Project Overview
- Client/Appointing Party: contact us to disclose
- Project Name: contact us to disclose
- Project Code: FPH035
- Location:
- contact us to disclose
Project Participants
- MEP Contractor: contact us to disclose
- MEP Consultant: contact us to disclose
- Building Services Manager: contact us to disclose
- Mechanical Coordinator: contact us to disclose
- Electrical Coordinator: PROJECT DESIGN (IO) LTD, 99 Church Hill Road, North Cheam, Sutton, Surrey SM3 8LL
- Nurse Call Specialist: contact us to disclose
Latest Work Statistics:
Total Time
This is the time we spent so far to produce drawings for construction. We are still waiting for Security Specialists comments and further changes to Level 3 plantroom containment due to mechanical changes
Work Statistics
- Total Time: 570hr 17min
- Planning: 4hr 18min
- Setting up Autodesk Construction Cloud (ACC) Coordination: 11hr 30min
- Building Special Families: 41hr 35min
- Technical Input: 30hr 14min
Coordination and Modelling (WIP and P01)
- Fire: 28hr 13min
- Lighting: 38hr 12min
- Nurse Call: 51hr 57min
- Security: 5hr 26min
- Small Power: 57hr 45min
- Coordination – Containment: 82hr 28min
- Coordination – Vertical Distribution (Risers): 5hr 33min
- Coordination – Equipment: 10hr 54min
- Coordination – Specialists: 2hr 1min
Changes Following Submittal of P01 Revision
- Coordination – Containment: 92hr 27min
- Coordination – Vertical Distribution (Risers): 10hr 57min
- Fire: 1hr 45min
- Lighting: 32hr 37min
- Nurse Call: 1hr 53min
- Small Power: 50hr 55min
Challenges and Solutions
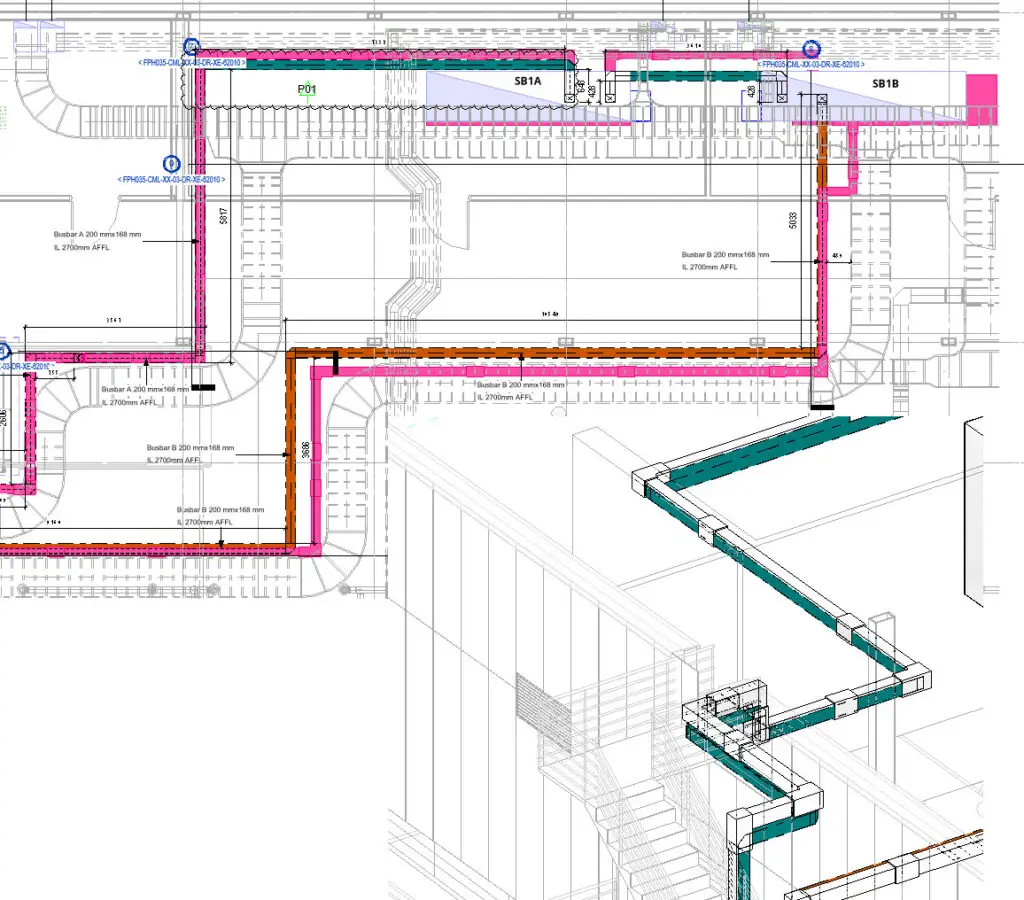
Incoming Supply 1600Amp Busbar
Compatibility Issues: The coordination of the cast iron main supply 1600Amp A & B bus bar was complicated due to compatibility issues between different software solutions..
Solution: We utilized Revit software to bridge the compatibility gap, ensuring accurate alignment with the building’s structural and architectural elements.
Vertical Distribution
Space Allocation Oversight: Consultant’s oversight in allocating space for Electrical Risers and Distribution Boards led to re-work impacting all services and architectural layout.
Coordination Disconnect: There was a disconnect between the Mechanical and Electrical teams in consultant’s team, leading to space conflicts.
Solution:
We collaborated closely with the Mechanical Coordinator and MEP Contractor to resolve space allocation issues, ensuring the correct routing and installation of sub-main distribution cables and distribution boards. Enhanced communication and coordination prevented future space conflicts.
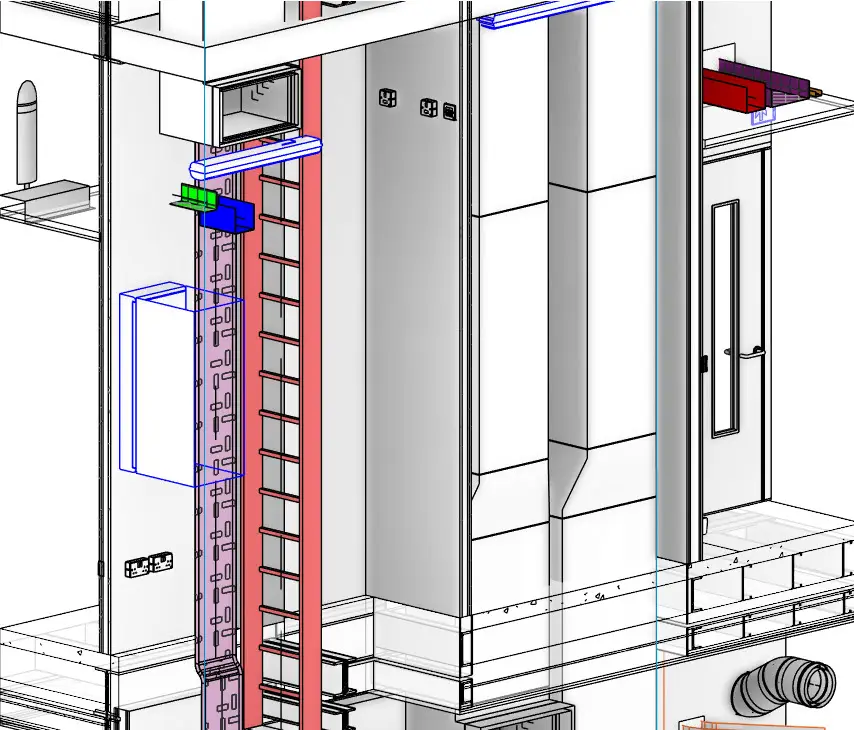
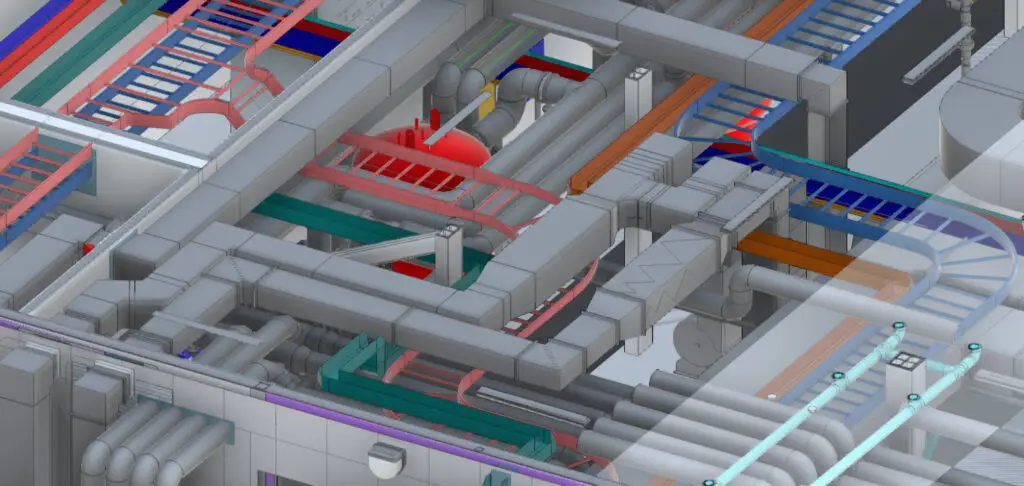
Plantroom Coordination
Mechanical Plant Space Constraints: The consultant’s MEP model contained generic mechanical plant, during detailed coordination, it became apparent that major re-design is required. This caused 12 weeks delay
Solution:
Collaborated closely with the Mechanical Coordinatior and MEP Contractor to find route for the cast iron 1600Amp busbars, cable ladders, electrical risers and sequence the coordination process to minimise delay.
Buffer Vessel Clashing
Buffer Vessel Clashing: The delivered buffer vessel was taller and wider than modelled, causing a clash with the proposed cable ladder.
Solution: We adjusted the cable ladder’s position and height based on the provided dimensions to avoid clashes. The ladder was moved 436mm to the left and kept at 2700AFFL, maintaining a 300mm space between the BusBar and ladder.
Early detection and continuous monitoring allowed us to address potential issues promptly, preventing a domino effect of changes.
Successful Coordination of Electrical Systems
Successfully integrated lighting, power, fire alarm, nurse call, and security systems within the project timeline.
Integration of Advanced Diagnostic Equipment
The project included the coordination of advanced diagnostic equipment such as MRIs, CTs, Gamma Cameras, and Mammography units.
Efficiency
Our coordination process led to significant improvements in the accessibility for maintenance
Effective Space Management and Allocation
The issue with space allocation for electrical risers and distribution boards was resolved early, although it did have an impact on the programme and architectural layout.
We understand
We have the experience and expertise to understand the complexities you face.
How We Make Your Life Better:
• Save Time: Our efficient processes mean fewer delays and faster project completion.
• Cut Costs: By avoiding rework and optimizing designs, we help you stay within budget.
• Expect Quality: Our expertise ensures that all systems are integrated smoothly and work flawlessly
What You Need to Do:
Contact us today to discuss how we can support your next project.
BIM Coordination
The project highlights the transformative potential of effective BIM coordination. Despite the project’s ongoing nature and challenges, the successful integration of complex MEP systems within the given constraint underscores our commitment to excellence.
Collaborative Efforts
Our adaptive strategy and collaborative efforts have not only ensured compliance and integration but have also delivered significant improvements in the coordination process.
Analysis
The initial coordination and modelling efforts were substantial, reflecting the project's complexity. The total time spent on primary coordination and modelling was considerable. However, the revisions following the P01 submission highlighted the dynamic nature of the project. Additional coordination, especially for containment, increased by over 50%, bringing the total revision time to a significant portion of the overall effort. This rework underscores the challenges faced and the rigorous efforts required to ensure compliance and integration.
Current Status and Ongoing Work
The Hospital project is still ongoing, with the installation phase in progress. The plant room area is undergoing further mechanical changes to address evolving requirements and ensure the integration of all systems remains seamless. Our team continues to adapt and coordinate efforts to meet these new challenges
Client Feedback
Positive feedback has been received from the Client, particularly highlighting the effectiveness of the coordination efforts and the minimal disruption caused to ongoing hospital construction.